Main
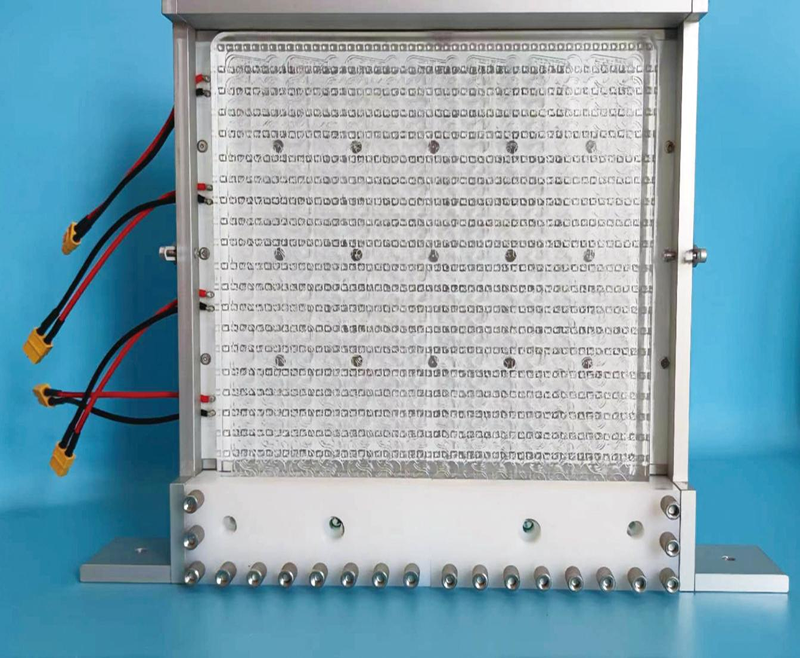
CM-DG & PG Photochemical Reactors
Function
Photochemical reactor is mainly applied to research gas / liquid phases, fixed / simulated visible light, Photochemical reaction under conditions of photocatalyst,etc.It is widely used in fields of Chemosynthesis, environment protection, life science, etc.The photochemical reactors can improve the efficiency of chemical synthesis, and can also perform reactions that would otherwise be impossible.Our photochemistry reactor is modular, flexible, scalable and easy-to-use, it makes modern photochemistry techniques accessible without the limitations of traditional batch requirements.The photochemical reactor system is appropriate for “free radical” reaction mechanism. Its application is highly popular in fields such as halogenations of organic compounds, production of primary mercaptans, oxidation, isomerizations, polymerizations, hydrogen generation, solar application, Photolysis of toxic wastes etc.Photochemistry is also used in the curing (polymerization) of specially formulated printing inks and coatings. Used in research and science, environment, green/clean energy, water splitting and so on. Our products are distinct, designed with an eye on easy operations and cleaning; optimum lamp spacing, uniform flow field, and significant efficiency advantages amongst others. The photo catalytic reactor is also used for derivatisation of Aflatoxins and enhanced detection.The CM-DG photochemical reactor makes photochemistry accessible. Eliminating the problems of traditional batch photochemistry, the CM-DG photochemical reactor allows the full potential of photochemistry to be exploited. It offers safe, precise, efficient, consistent and scalable photochemistry under continuous flow operation.The narrow channel dimensions of flow reactors provide opportunities to ensure a uniform irradiation of the entire reaction mixture. Consequently, photochemical reactions can be substantially accelerated and scaled to higher quantities compared with batch reactors. Flow chemistry is also the technology of choice for transformations involving multiple phases. The high surface-area-to-volume ratios are a consequence of the small reactor size, leading to efficient mass transfer between two (or even three) phases. In case of gaseous reagents, flow reactors further offer the opportunity to control the stoichiometry of gasses with mass-flow controllers and are easily pressurized, which increases the solubility of gasses in the reaction mixture.Concerning the light input we count on energy-efficient LED technology. The small size of the LEDs and their relatively low waste heat allow for a targeted adaption of the lighting units to any particular microreactor class. A further special advantage of these light sources is their quasi-monochromatic light emission, allowing a very selective excitation of the photochemically active material.
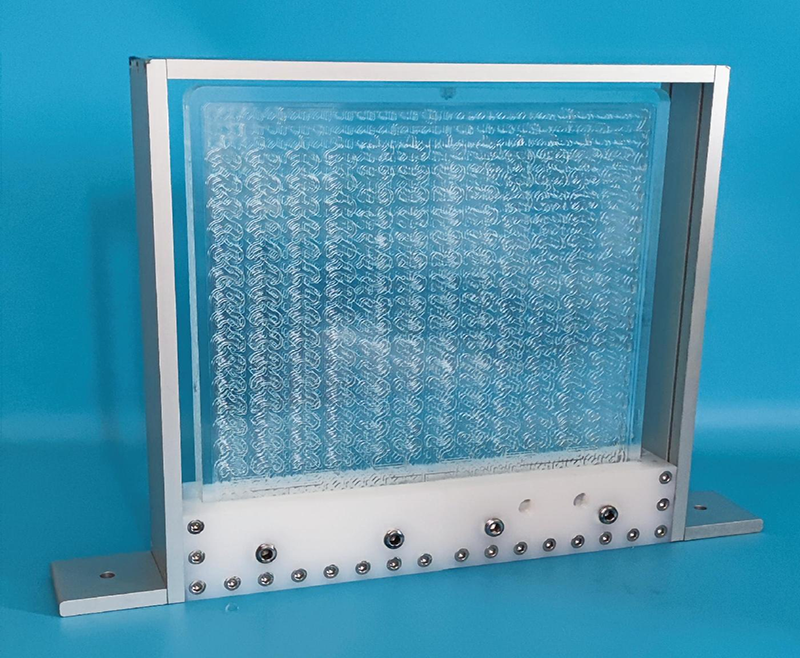
CM-P Pilot-scale & Production-scale Glass Flow Reactor
Function
CM-P is a modular, glass flow reactor for process development, pilot & full-scale production. Fabricated from borosilicate glass, with integrated heat exchange, MF-V9 flow reactor modules give unrivalled chemical compatibility & process control for challenging chemical applications at scale.Employing standard tube fittings, MF-V9 flow reactor can be used with existing pumps & thermostats, or supplied as total systems on request.
Our industrial flow reactors are modular glass reactors for the performance of continuous flow reactions at ton scale.Microchannel reactors are suitable for chemically challenging reactions under extreme processing conditions such as fast, highly exothermic reactions, reactions with aggressive media, reactions employing unstable intermediates or hazardous reactions not accessible under batch conditions.
The CM-P thousand-ton glass microreactor is a capacity upgrade without magnification structure based on the CM-D small scale glass microreactor. Compared with CM-D, CM-P does not amplify the former unit hybrid structure to the same proportion, but transfers the unit hybrid structure of CM-D in parallel with 8 threads without amplification. Through the special design of 3-layer heat exchange, 2-layer process, and 1-layer sealing, the flux is increased by 15-20 times, and the heat exchange efficiency is further strengthened, so that the reaction can still be obtained in the case of high flux Good heat transfer control. At the same time, the two major factors of mass transfer and pressure drop are taken into account, ensuring mass transfer without amplification effect and small pressure drop, realizing the maximization of mass transfer and heat transfer efficiency, and safely and stably achieving the thousand-ton pilot production process.
CM-P, liquid holding capacity 100mL, 8-pass parallel connection, 6-layer 3 heat exchange 2 process design, flux can reach 1500-2000T/a, support UV light penetration above 315nm UVB (80% light transmittance) , and the same flow pressure.
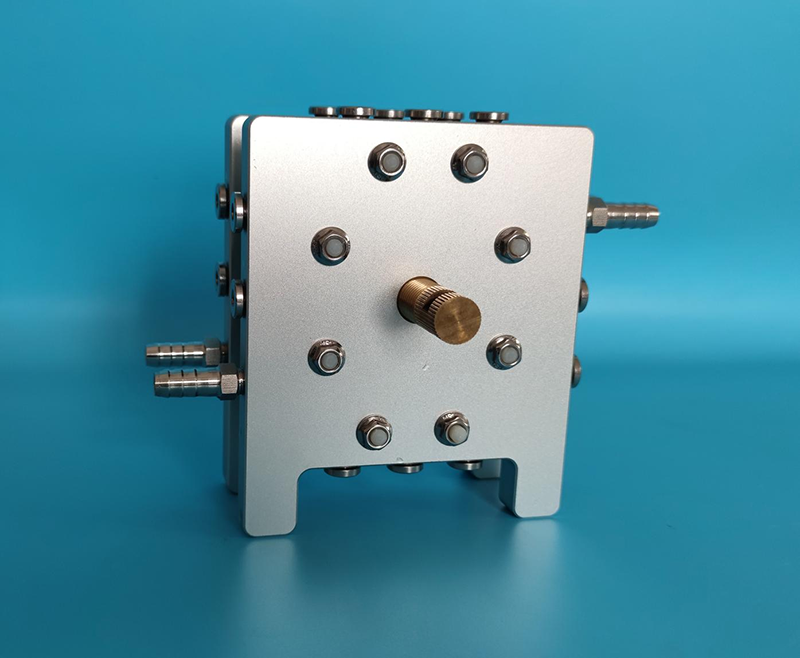
CM-Elflow Electrochemical Reactor
Function
Electrochemical synthesis is the use of electrical energy to drive chemical change; using electricity to replace toxic and costly chemical reagents. This allows cleaner and cheaper syntheses with greater production efficiency and at reduced cost.
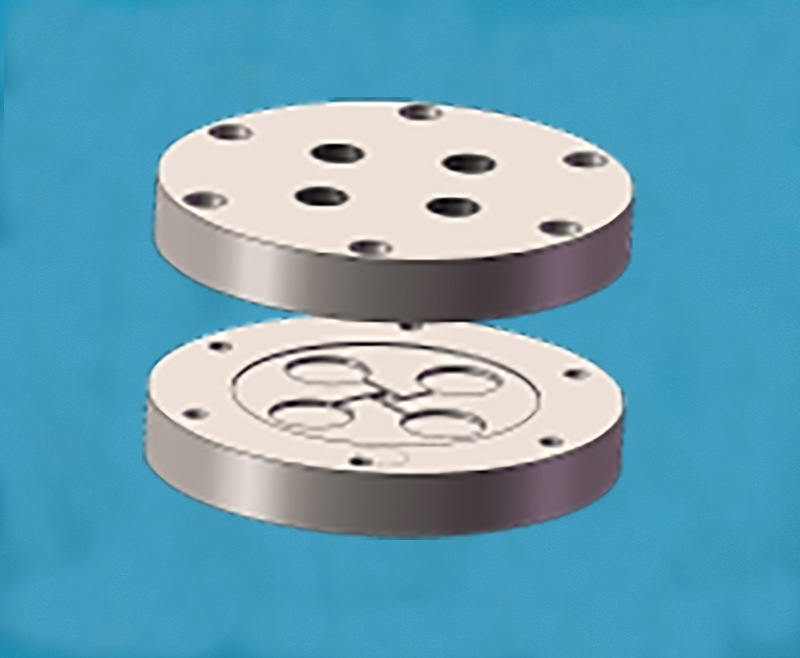
CM-X Series Static Micromixers
Function
Compared with the traditional tank type dynamic stirring mixing and pipeline static mixer, the micro mixer has the advantages of large specific surface area, high mass and heat transfer efficiency, high safety, and small amplification effect. In the process of reaction amplification and optimization, the microchannel mixer has higher reproducibility, stability, and high efficiency. In the case of blocking conditions, due to the special sealing and packing design, compared with the traditional The pipeline static mixer is easier to clean the dirt and replace the mixed filler. As a special form of the microreactor, the micromixer can handle many processes that cannot be handled by other equipment in the continuous flow process.
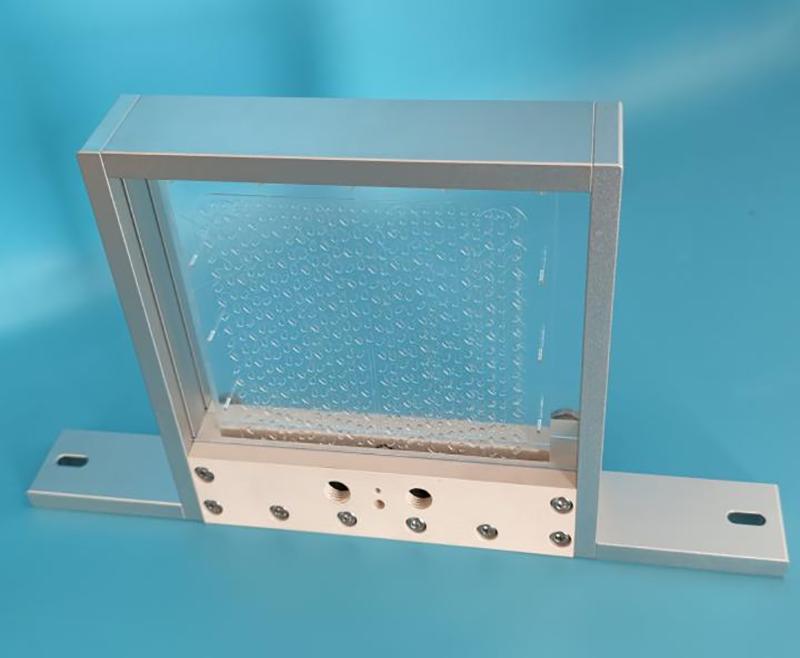
CM-D Series Kilo-scale Glass Flow Reactor
Function
The CM-D series continuous flow reactors is a high-throughput glass microreactor processed from high borosilicate float glass. The four-layer structure design includes the heat exchanger in the reactor to reduce the space occupancy rate. The design of the structure ensures the maximization of mixing efficiency, so that the reaction phase forms multiple vortex staggered states in the reaction phase, and ensures that the reaction phase is fully mixed and reacted in the flow channel.
The CM-D series glass microchannel reactor is compatible with all reagents except hot concentrated alkali, molten alkali metal, hot concentrated H3PO4, HF, and strong corrosive agents. It can operate stably for a long time. The excellent high light transmittance can achieve short wavelength Photocatalytic reaction. Compared with the traditional tubular catalysis, the microreactor can also increase the catalysis conditions and promote the formation of reactants through the application of the heat exchange layer.
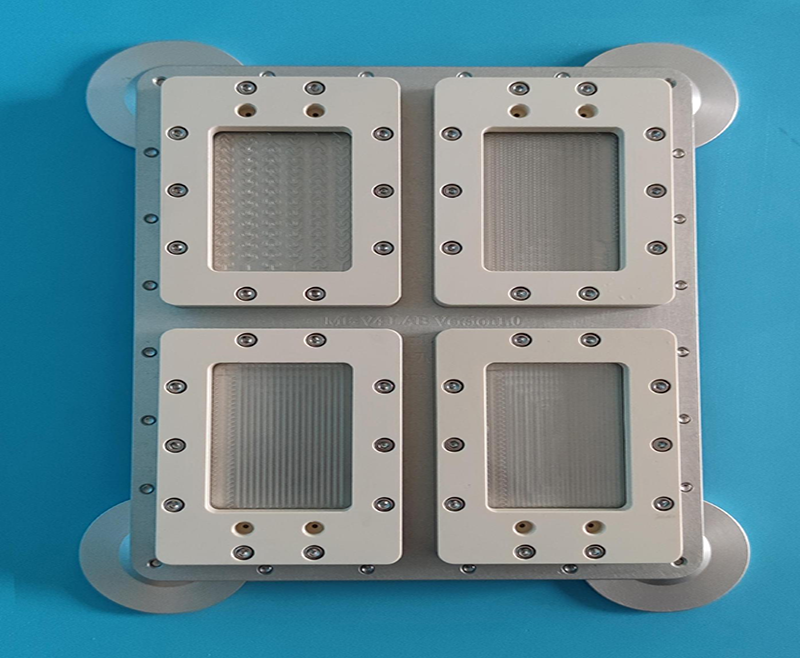
CM-T Series Lab-scale Glass Flow Reactor
Function
CM-T is a manually operated, metal-free continuous flow microchannel reactor system for reaction screening & process optimisation. Its modular design gives the user flexibility on the number of feed lines, reactor type & volume.With glass microchannel reactors at the heart of the system & peripherals with a high chemical compatibility, the lab-scale system is suitable for a wide range of challenging chemistries & processing conditions.
The microreactor has the advantages of large specific surface area, high mass and heat transfer efficiency, high safety, and small amplification effect. Compared with the traditional batch reaction, it has higher reproducibility and stability in the process of reaction amplification and optimization, sexuality and efficiency. In addition, the micro-reactor has a low heat buffer demand, a small footprint, and a high degree of automation, which greatly saves manpower and material resources.
CM-T series glass microchannel reactors have the characteristics of low reagent consumption (liquid holding capacity of microliters), large specific surface area, high temperature resistance (-25℃~195℃), high pressure resistance (2Mpa), etc. The product takes into account the two major factors of mass transfer and pressure drop. There is no sudden shrinkage and sudden expansion in the process flow channel, which ensures efficient mass transfer and small pressure drop. The heat exchange module can maximize the mass transfer and heat transfer efficiency. Safely and stably realize the chemical process of research and development and small-scale trials.
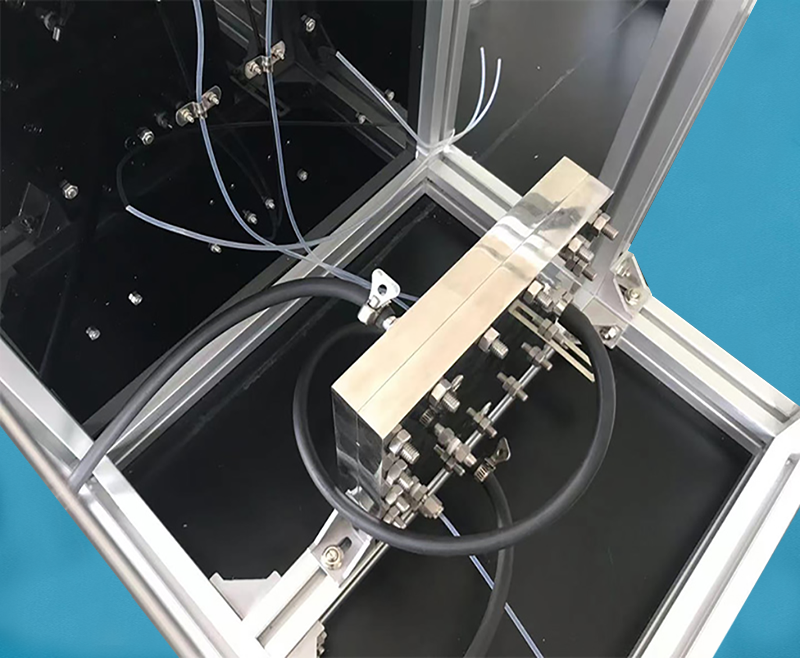
CM-DM&PM Flow Microchannel Reactor(Metal)
Function
For Lab Research and lab scale productions. Switch batch production to continuous production, solving the major hazards of explosion, low efficiency, severe pollution and large energy consumption. Extremely Exothermic Reactions.High Temperature, High Pressure Reactions.Polymerization